Laying plastic pipes successfully: how WKT ensures quality right from the start
In this article, we take a look behind the scenes and show what needs to be taken into account when laying our plastic pipes in order to fulfil the highest standards.
Durability, corrosion resistance and versatility - these are the typical requirements for high-performance plastic pipes. As a manufacturer and producer, we know that the quality of a product depends not only on the material, but also on professional processing and installation. Every installation is a crucial step in ensuring the service life and performance of our high-quality plastic pipes in the finished pipe system. You can find out more directly in our download area under ‘Instructions for use’.
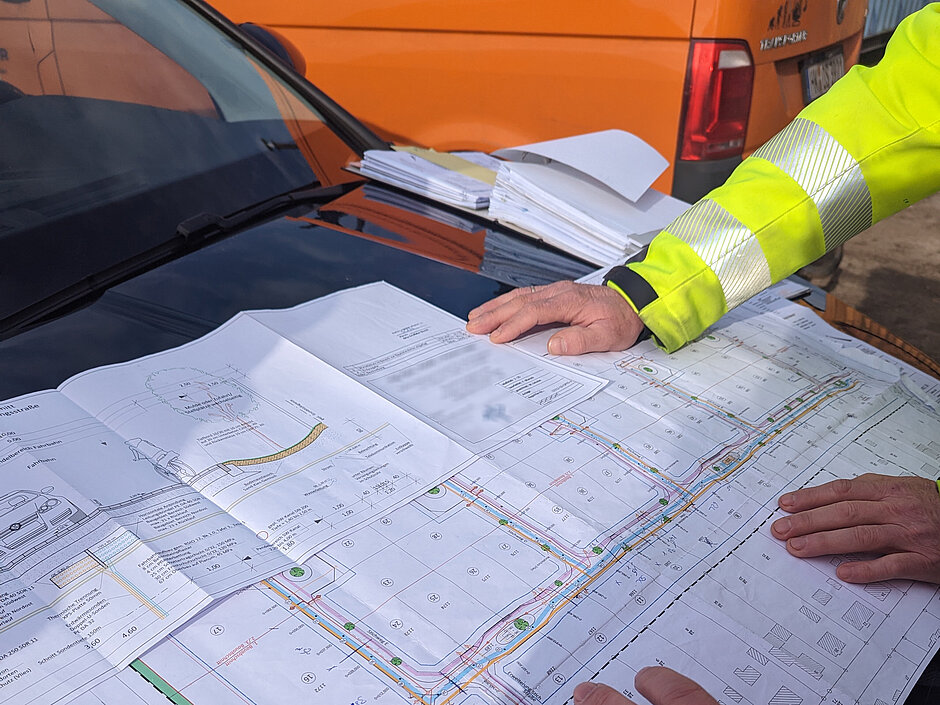
Thorough planning for smooth processes
Even before a single pipe is scheduled for production on our machine, everything starts with detailed planning. Your specialist planner analyses the operating conditions in detail to ensure that each pipe system is optimally matched to the requirements on site. This is also where the planner determines which material is to be used - the concrete comparison of the physiological properties of the various materials naturally serves as a decision-making aid.
Focus:
- Determining the installation location
- Investigation and definition of the requirements for the subsequent pipe system (including planned pressure, expected operating temperature, external influences, medium to be conveyed)
- Selection of suitable pipe material (tailored to your requirements)
- Consideration of possible environmental influences (soil composition, risk of frost, UV radiation, etc.)
- Coordination of the installation method
- Preparation of a suitable storage area
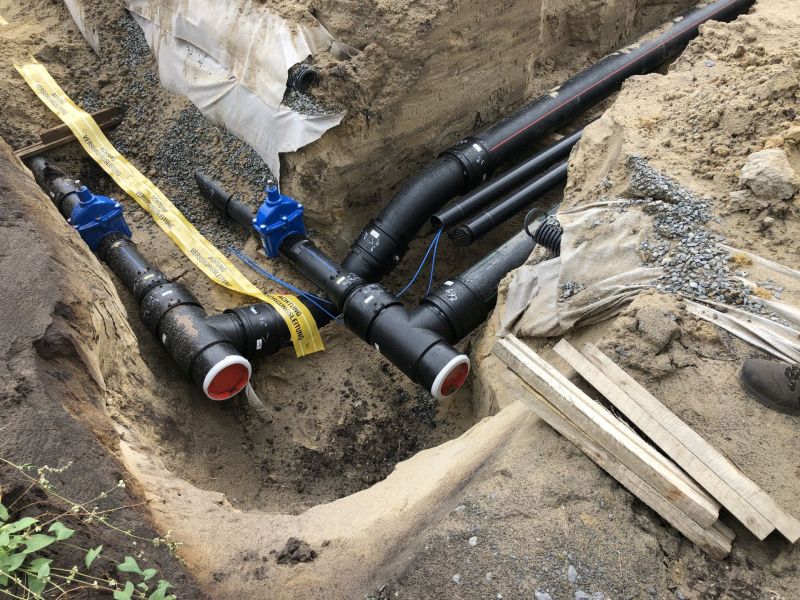
Perfect connections for maximum tightness
Even the longest or straightest pipe system cannot do without joints. Depending on the dimensions, this may only be the case with PE pipes after more than a hundred metres (as they may be in drums) and with PVC pipes after 6 metres at the latest. Whether welding, gluing or mechanical joining - every connection must be able to withstand the highest loads to be expected in later use. Every step should therefore be checked precisely to avoid subsequent stresses or even leaks in the system.
This is what matters:
- Welded joints (e.g. for PE pipes): Exact adherence to the welding parameters (temperature, time and pressure)
- Adhesive joints (e.g. PVC-U): Use of specially formulated adhesives and strict adherence to the manufacturer's specifications for dosing and curing time
- Mechanical connections: Regular inspection of the sealing rings and careful tightening of the joints
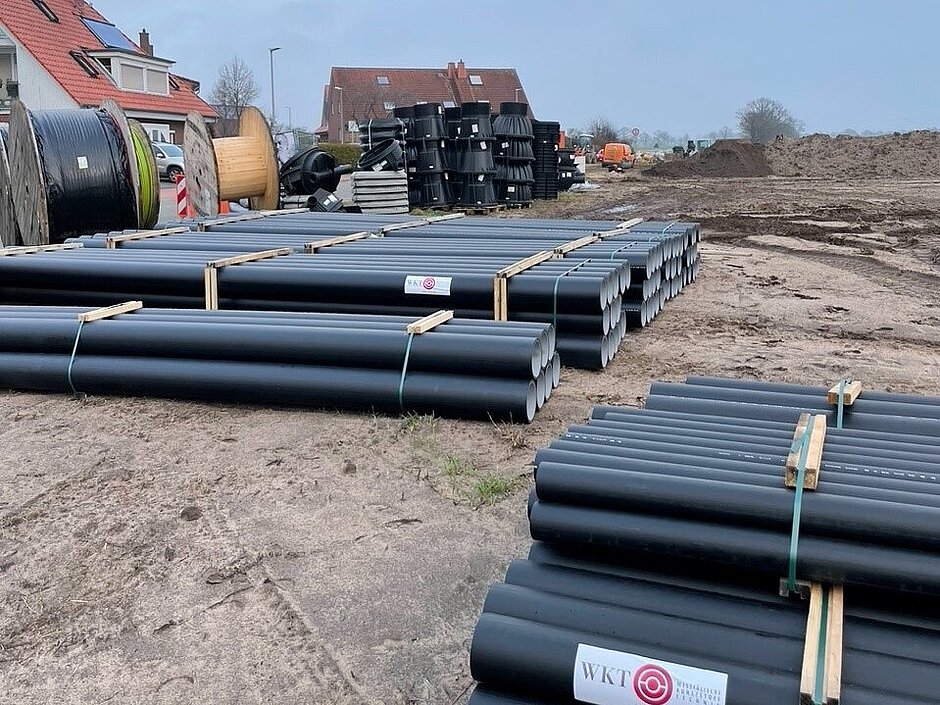
Securing the installation conditions
Correct pipe installation requires not only care, but also the correct preparation of the surrounding area. For this reason, the conditions on site should be optimised to prevent damage.
The standards:
- Storage of the plastic pipes on a level surface, palletised pipe bundles can (only) be stored stacked if the pallet timbers are placed on top of each other
- Take into account possible thermal (linear) expansion of the plastic pipes, especially at extreme outside temperatures (frost or extreme heat); in this context: if necessary, also pre-storage of e.g. moulded parts before installation
- Remove sharp objects from the installation area to protect the pipes from mechanical damage
- Compliance with the permitted bending radii to avoid stresses or material damage and - depending on the material used - planning suitable expansion bends
- Laying below the frost line, especially for drinking water and waste water pipes

Testing and quality assurance
Even after professional installation, the installation process is not yet complete. Before commissioning, a thorough check of the entire system is essential.
Quality assurance measures:
- Carry out pressure tests to check for leaks and resilience
- Visual inspection of all connections and transitions for potential weak points
- Documentation of the results for maximum transparency and traceability
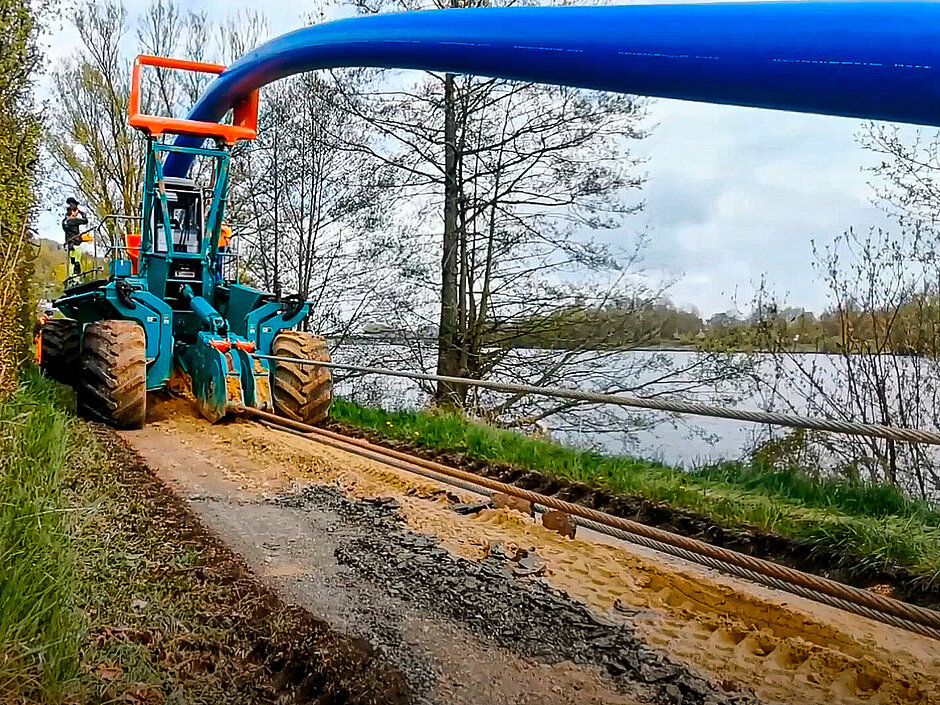
Sustainability and future security
As a company that is committed to environmental protection - and to the principles and strategies of the UN Global Compact - we attach great importance to sustainable installation practices. Our aim is to play our part in creating pipe systems that are not only durable, but also conserve resources.
Our contribution:
Optimising installation to minimise material waste
Production of pipe types that are 100% recyclable and meet the requirements of the circular economy
Quality assurance in the production of plastic pipes with a service life of up to 100 years
Quality that starts with the installation
Laying plastic pipes is more than just a work step - it is a decisive factor for the performance and service life of an entire pipe system. With a clear strategy, state-of-the-art processes and the highest quality standards, WKT ensures that pipe systems not only function reliably today, but also in decades to come. We are proud to be able to apply these values to every single project - from planning to the final connection.
Would you like to find out more about how we work and how to choose the right product for your construction project? Then contact us at any time - the WKT team is on hand to advise you and looks forward to hearing from you!